In the world of manufacturing, sheet metal fabrication stands out for its versatility and precision. Customization plays a crucial role in meeting specific design requirements, allowing businesses to create tailored solutions for their projects. This article explores the intricacies of the customization process in sheet metal fabrication, shedding light on techniques, tools, and best practices that ensure optimal results. Understanding this process not only enhances product quality but also drives efficiency and innovation in various industries.
Overview of Sheet Metal Fabrication
Sheet metal fabrication involves the manipulation of flat sheets of metal into desired shapes and sizes through various processes. The main processes used in sheet metal fabrication include cutting, punching, bending, and welding. Each technique plays a crucial role in creating components for industries such as automotive, aerospace, and construction.
Customization is central to sheet metal fabrication. Clients often provide specific design requirements, which can include dimensions, materials, and finishes. Advanced tools, like CNC machines and laser cutters, improve precision and allow for tailored solutions.
Understanding the flow of the sheet metal fabrication process aids in optimizing production. The typical workflow starts with design, where engineers create detailed drawings or computer models. The next stages involve material selection and preparation. After that, cutting, forming, and assembly occur to produce the final product. Quality control inspections ensure specifications are met before distribution.
The use of simulation software during the design phase helps predict potential issues. This proactive approach can reduce material waste and minimize errors during production, leading to cost savings and improved efficiency.
Sheet metal fabrication combines various techniques and modern technology to meet specific design needs, demonstrating its importance in multiple manufacturing sectors.
Importance of Customization
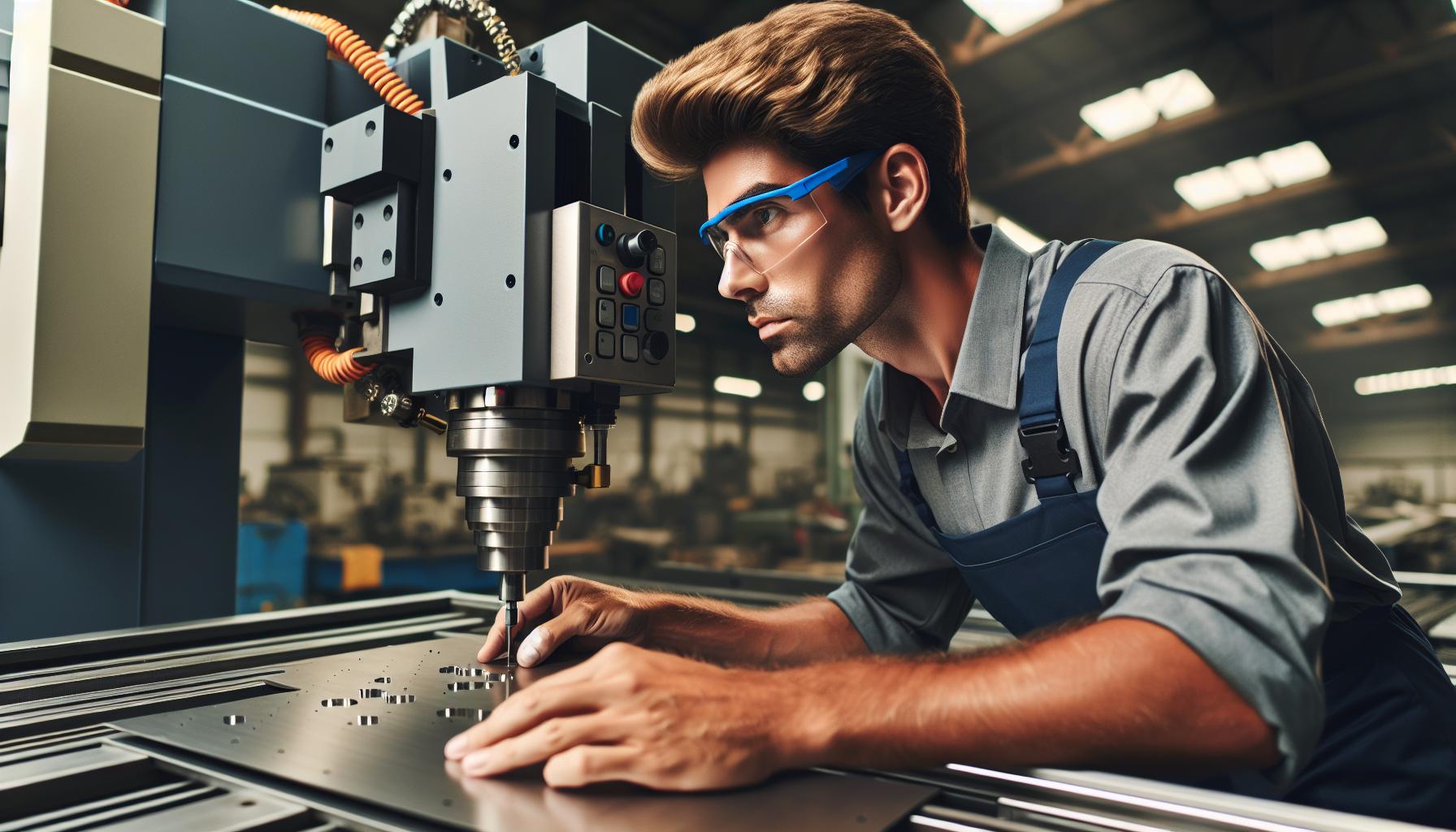
Customization plays a crucial role in sheet metal fabrication, allowing businesses to create unique and tailored solutions. It enhances design flexibility, ensures products meet specific requirements, and supports innovation across industries.
Benefits of Customization
- Precision: Customized sheet metal components achieve tight tolerances and precise measurements. Advanced tools ensure that designs translate accurately from concept to reality.
- Efficiency: Custom solutions streamline production processes. Tailored designs reduce waste, minimize rework, and optimize material usage.
- Quality Enhancement: Custom fabrication allows for better integration of components, improving overall product quality. This focus on detail strengthens structural integrity.
- Market Differentiation: Unique designs help businesses stand out in competitive markets. Custom products can cater to niche markets effectively.
- Automotive Industry: Customized metal parts are integral to vehicle manufacturing, including frames, brackets, and body panels.
- Construction Sector: Building components, such as steel beams and custom enclosures, often require precise specifications to meet structural needs.
- Manufacturing Equipment: Equipment manufacturers utilize customized sheet metal for machinery covers, housings, and guards, aligning with specific operational requirements.
- Aerospace: Components in aviation often demand custom fabrication to accommodate performance, weight, and safety standards.
Steps in the Customization Process
The customization process in sheet metal fabrication comprises several clear steps, ensuring precision and quality from initial design to final product.
Designing the Specifications
Designing specifications begins with gathering requirements from clients or stakeholders. Designers utilize computer-aided design (CAD) software to create detailed blueprints that outline dimensions, shapes, and functional features. Accurate specifications ensure the final product meets all functional and aesthetic criteria.
Selecting Materials
Selecting materials involves choosing the right type of metal based on the project’s needs. Common options include aluminum for lightweight projects, stainless steel for corrosion resistance, and carbon steel for strength. The selected material plays a vital role in the durability, weight, and performance of the final product, influencing both functionality and cost.
Fabrication Techniques
Fabrication techniques encompass various processes that transform flat sheets into specified shapes. Common techniques include:
- Cutting: Mechanical saws or laser cutters are used to achieve precise shapes.
- Bending: Press brakes bend metal sheets into desired angles and dimensions.
- Punching: Punching machines create holes or cutouts for functional requirements.
- Welding: Welding joins different metal pieces together, ensuring structural integrity.
Each technique contributes distinctly to the customization while adhering to the design specifications.
Quality Control Measures
Quality control measures ensure the final product meets all applicable standards and specifications. Inspection at various process stages may include:
- Dimensional Inspections: Measuring each part against specifications to ensure accuracy.
- Visual Inspections: Identifying surface defects or imperfections.
- Functional Testing: Verifying that the product performs as intended.
Effective quality control processes help maintain high standards, ensuring every custom component delivers reliability and performance.
Challenges in the Customization Process
Custom sheet metal fabrication faces several challenges, impacting product quality and production efficiency.
Technical Limitations
Technical limitations play a significant role in the customization process. Specific materials may not withstand certain forming techniques, leading to structural integrity issues. Equipment constraints can restrict complex designs, as not all machinery accommodates intricate patterns or tight tolerances. Material thickness influences machining capabilities, thereby determining the extent of customization. Additionally, software limitations in design can prevent accurate simulations, resulting in unforeseen complications during production.
Cost Considerations
Cost considerations also affect the customization process. Unique designs often require specialized tools or additional labor, raising production costs. Material selection impacts budget constraints, as some metals are more expensive than others. Small production runs can result in higher per-unit costs due to setup expenses. Balancing quality with affordability remains a challenge, as businesses aim for customized solutions without exceeding financial targets. It is necessary to evaluate the return on investment when considering custom-made parts versus standard options.
Conclusion
The customization process in sheet metal fabrication is essential for meeting diverse industry needs. By leveraging advanced techniques and tools, manufacturers can produce tailored solutions that improve product quality and performance. Understanding the intricacies of this process not only improves efficiency but also fosters innovation across various sectors.
As businesses navigate the challenges of customization, balancing quality with cost remains crucial. The ability to create unique designs provides a competitive edge while ensuring that products meet specific requirements. Ultimately, embracing customization in sheet metal fabrication leads to better integration of components and drives success in an constantly changing marketplace.
Frequently Asked Questions
What is sheet metal fabrication?
Sheet metal fabrication is the process of manipulating flat sheets of metal into specific shapes using techniques like cutting, bending, punching, and welding. It plays a crucial role in various manufacturing sectors, allowing for the production of customized metal parts.
Why is customization important in sheet metal fabrication?
Customization is vital because it allows businesses to meet specific design requirements. This process enhances design flexibility, ensures precision, and fosters innovation, making it easier for companies to differentiate themselves in competitive markets.
What techniques are used in the customization process?
The customization process includes several techniques such as cutting (using laser or CNC machines), bending, punching, and welding. Each method is essential for accurately achieving the desired shapes and specifications of the final product.
How does simulation software improve the customization process?
Simulation software helps predict potential issues during the design phase, reducing material waste and improving efficiency. It allows manufacturers to test and refine their designs before production, ensuring better outcomes and reducing the likelihood of errors.
What materials are commonly used in sheet metal fabrication?
Common materials include aluminum, stainless steel, and carbon steel. The choice of material affects the final product’s durability, performance, and suitability for specific applications, so selecting the right one is crucial.
What are the quality control measures in sheet metal fabrication?
Quality control measures include dimensional inspections, visual assessments, and functional testing. These steps ensure that the final product meets applicable standards and delivers the reliability and performance required by clients.
What challenges are faced during the customization process?
Challenges in the customization process may include technical limitations, such as material constraints and equipment capabilities, which can restrict complex designs. Additionally, unique designs often lead to higher production costs, necessitating a balance between quality and affordability.
Which industries benefit the most from customized sheet metal parts?
Industries like automotive, construction, manufacturing, and aerospace greatly benefit from customized sheet metal parts. These sectors require tailored solutions for components that must meet specific performance and design standards.